Production and Quality Record System – Access Application
An example of Access Application Development includes this Production and Quality Recording System.
Customer
Technical Service Consultants Ltd (TSC), a clinical company and global supplier of swabs and microbial consumables based in Lancashire, United Kingdom (UK).
Profile
Since 30 years, TSC has been manufacturing high quality products in UK for use in pathology laboratories and applications across the world. Their product range is widely used in sample collection, transport identification and storage to obtain accurate results. They began their work in the clinical field with dry swab collection kits and Probact transport swab systems. Today, TSC possesses the most extensive range of swabs to meet requirements ranging from paediatric to large animals. The company takes keen interest in innovations and evolving products based on customer feedback. TSC created the first bacterial bead preservation system, Protect, along with products for bioluminescence (ATP) testing. TSC also operates its own plastic injection moulding company under the Goodbrand Plastics brand.
Project Title
Production and Quality Record System (PAQRS)
Project Summary
A multi-user application was required to administer Production Flow Control system. It should be capable of managing product, batch, irradiation and quality control records on the production line.
Technologies Used
The application was developed using Access 2000 Forms and Visual Basic for Applications (VBA). An Access database resided at a centralized server for client Access applications to connect to it over the network.
Solution Description
Challenge
TSC was looking to completely restructure their existing system for collecting, and recording data , and generating reports. Their conventional way of managing production and quality records was becoming too costly and time consuming.
The scope of the project was to design a system that could be deployed in a multi-user environment with all the data stored at a centralized database. They were not looking to make a large investment in technology and were seeking a solution that did not require the purchase of additional IT infrastructure.
The challenge was to design a custom application which would fit in effortlessly with their existing method of managing production data. The new system would have to be simple to set up and administer but be capable of automating all activities involved in their production line. It was essential that the system be consistently efficient and error-free. And all manufacturing and production data should be accessible from multiple locations.
Solution
A customized Access application was designed to create a centralized data repository with simple, intuitive screens for tracking user information, entering and updating production, manufacturing and quality records.
The system was divided into various sections to enable easy and quick access to all kinds of data.
- A new user could be created by the System Administrator and granted access rights as desired to the relevant parts of the system. After successfully signing in to the application, the user would be directed to the Home screen which shows all the available modules and action buttons enabled/disabled based on the role of the logged in user.
- User Account Management section was designed to handle all user related information. Users and administrators would be able to create, update and delete data as per their requirements.
- With the help of the Product Management module, a user would be capable of creating product information and editing existing product data.
- Using Irradiation Management section, a user would be able to work with irradiation batch and certificate details.
- In the Batch Processing module, users would be able to create new batch records, manage existing batch records, reprint production sheets, enter raw material details and update the quality control test results.
- The Print Release Sheets section would enable users to print details corresponding to multiple irradiation batches.
Result
The completed PAQRS enabled multiple users to create batch records with product details and record its irradiation status report. It also allowed users to edit existing batches, products and irradiation reports. Direct database editing was restricted for system users with the exception of the system administrator.
Some useful features available with the implementation of the system were:
- Central administration for application and database
- Fairly simple and intuitive system interface
- Ability to extract specific records for detailed quality analysis
- Assign rigorous testing procedures for select records
- Generate accurate analysis reports
Below are some sample screens of the application:
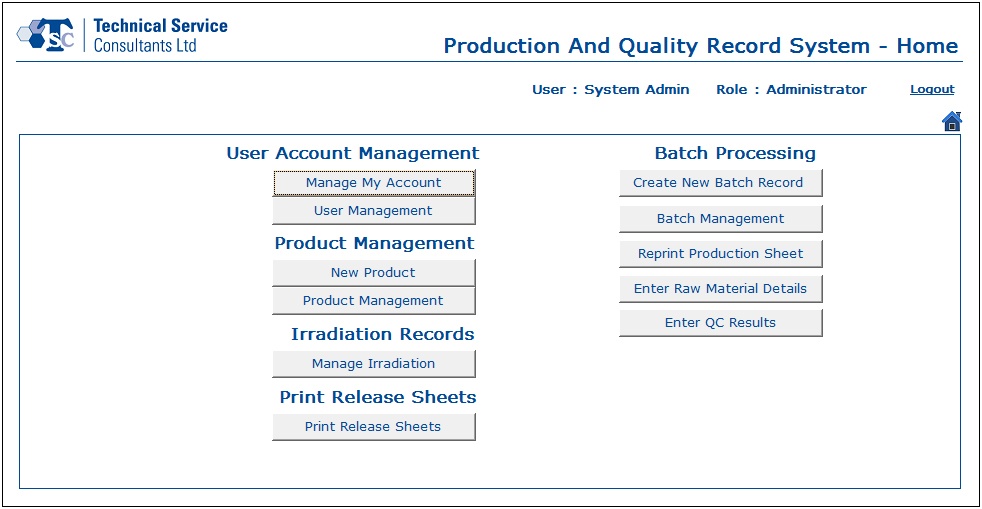
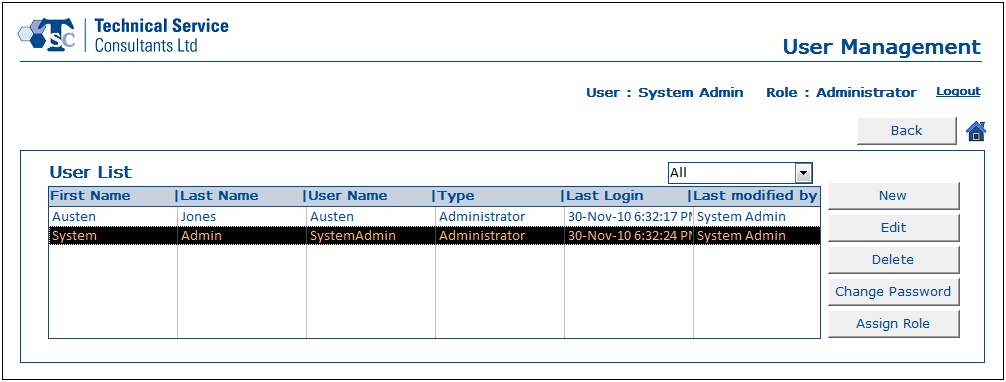



Delivery
The application lifecycle covering system redesign, development, testing and delivery was accomplished within a time frame of 4 months.
Benefits
By obtaining a bespoke application, TSC was able to implement a system that worked exactly as per organization’s needs but without any unnecessary components. The software was designed specifically according to their requirements and this resulted in the system users performing the same amount of work in significantly less time. TSC users were able to closely monitor and report all production line data. This directly enabled TSC to reduce costly errors, improve efficiency and service delivery. Additionally, it helped them to reallocate resources to other important functions.
Some key advantages following the implementation of the system were:
- Instantly access all product records from any machine on the network and only to authorized users
- Considerable reduction in risk of manufacturing defective lots
- Implementation of newer testing procedures in significant less time
- Decline in costs of managing poor quality products
- Seamless updates and support for customizable process workflows